Protecting waterways is a top priority and key requirement for any exploration drilling program. Each and every drill site needs to source large volumes of water to run the drill, contain drill cuttings and prevent contaminated water from leaving the site.
Using less water, recycling fluids on site and reducing the risk of a spill are important considerations in the development of future drilling technologies.
Closed-loop systems meet all these criteria and make it possible to use up to 90 per cent less water on a drill site, plus eliminate the risks associated with open sumps.
“Closed-loop systems provide a mechanism for addressing environmental and community concerns about water consumption and discharge of water from drill sites,” explains Marke Wong, environmental superintendent at Huckleberry Mines and chair of the A ME BC Environment, Health and Safety Committee.
At sites near sensitive aquatic systems with valued natural resources, such as fish spawning areas or drinking water supplies, providing an option for a closed-loop system may be the difference between permit approval and costly delays.
“Exercising good environmental practices during the early stages of project development can translate into stronger community support and help in maintaining a social license to operate in later project stages,” says Wong.
Closed-loop drilling has already changed the way the oil and gas industry approaches solids control and waste management. It is a requirement of uranium exploration in many locations, too, but is now increasingly being used on mineral exploration projects to dramatically lower the amount of water used on a drill site.
Hy-Tech Drilling Ltd., based out of Smithers, B.C., is using its prototype centrifuge to recycle and reuse water on Pretium Resources Inc.’s 100-per-centowned Brucejack project, near Stewart in northeastern B.C.
“We run a closed loop system to reduce the number of litres used. The system is applicable to places where there is a water shortage or in environmentally sensitive areas,” explains Mick Murphy, environment, health and safet y manager at Hy-Tech Drilling Ltd. “There is more focus on managing return water and cuttings from the drill though settling tanks.”
Closed-loop drilling requires some extra gear, including a centrifuge and generator, explains Murphy. In a closed-loop drill system, drilling fluids are recovered and sent through a shaker. A high-speed centrifuge then spins the material to separate water from solids. Liquids that are normally sent to the sump pits are then reused for drilling on site.
The benefits of using closed-loop drilling on a mineral exploration project are considerable. Messy and dangerous sump pits – which take time and money to dig, maintain and decommission – are eliminated. Less water is extracted from potentially sensitive waterways or trucked in, and money is saved on materials used to mix mud. The efficiency of the drilling process is increased. The environmental benefits of closed-loop drilling systems are increasingly being recognized worldwide. In July 2014, the Australian Mud Company (AMC) was awarded the Association of Mining and Exploration Companies Environment Award for its unique solids removal unit (SRU). Drilling fluids are circulated directly from the drill collar to the SRU’s shaker, then drill solids are removed via the centrifuge. Cleaned drilling fluids are then returned to the drill hole. “The SRU was developed with our customers to reduce their environmental footprint while enhancing the efficiency of their drilling operations,” says Craig Weston, general manager, Asia Pacific, for AMC . The unit has demonstrated significant reductions in water usage, site rehabilitation and contamination risks – at some sites, customers have achieved a 90 per cent reduction in water.”
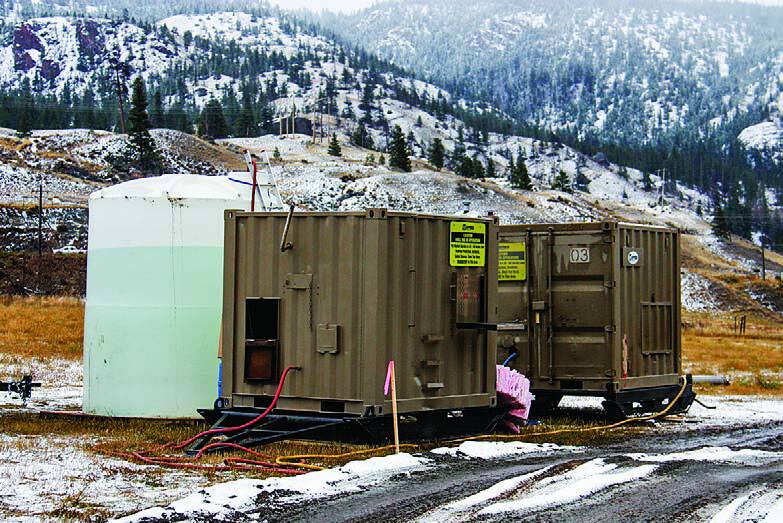
Early-stage exploration projects typically do not generate any revenue. They often have relatively small budgets and companies can be reluctant to engage communities or conduct environmental monitoring unless it is a permit requirement, explains Wong. “[But] if a community perceives a company as unwilling to communicate or accommodate their concerns, this can set up a confrontational situation, which may be difficult to overcome down the road. In some cases, utilizing a system like closed-loop drilling and conducting a basic environmental monitoring program appropriate to the scale of the project can provide the confidence to regulators and the community for expediting appropriate project approvals.” •