The world of printing has finally caught up with the real world – and if the displays at the PDAC convention in Toronto this year were anything to go by, 3D printing is finding its way in the mineral exploration industry. 3D printing, or additive manufacturing, has been around since the 1980s and is essentially the creation of a three dimensional object by laying down successive layers of material under the control of a computer. These materials are commonly plastic but can be metal, clay, sugar and even living cells.
The uses of 3D printing seem limited only by the human imagination. Already, high-tech engineering firms are using 3D printing for the rapid creation of prototype parts – many auto racing teams such as those in the technological bleeding-edge Formula One series now employ 3D printers rather than model makers to create parts for wind tunnel testing. The additive manufacturing process has also opened the possibility of creating components whose geometries are simply too complex for traditional machining or fabrication techniques. Although significant application to human medicine may be a few years off, enterprising and innovative animal rescue workers have already employed 3D printing to craft prosthetic legs for injured ducks. One project that has dominated headlines is the infamous Liberator, the world’s first operational 3D-printed gun.
International geoscience company CGG has already recognized the potential of 3D printing as a rapid and costeffective way to produce detailed 3D Earth models. These printed 3D Earth models offer a novel way of integrating all the geophysical and geological data available with respect to a target area for hydrocarbon or mineral exploration to highlight the distribution of prospective lithologies. As Reece van Buren, chief geophysicist with CGG Airborne, explains, “The advent of 3D print technology has really opened up new possibilities for us to literally ‘show’ our clients the power of geophysics for imaging what cannot be seen in the Earth’s subsurface.
We call it ‘your basin/target in a box,’ now available across our range of geophysical solutions. It’s a fantastic medium that’s accessible to all and offers a whole new visual and tactile experience.”
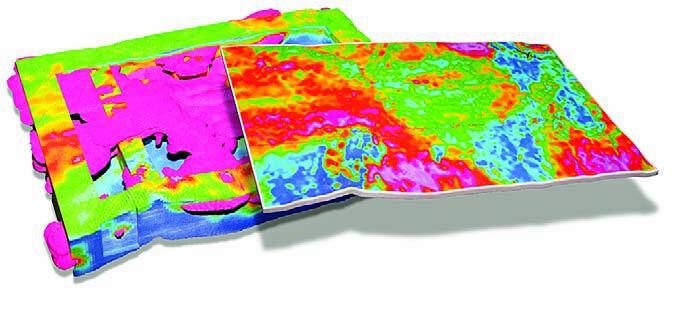
Van Buren adds, “Not only do we display these printed 3D Earth models on our booths at tradeshows to attract attention, we’re also distributing them to clients when they might assist their exploration discussions or negotiations. It really is a ‘wow’ moment when a geologist picks up their target, literally in the palm of their hand. Clients have commented on how natural it feels to be able to inspect their data in this fashion.”
Of course, the communication power of three-dimensional, physical models has long been recognized within the resource sector, and many such have been created over the years to showcase ore deposit geometries, pit outline and infrastructure layouts, as well as mill and processing circuit operations. However, these models are extremely timeconsuming and costly to manufacture, requiring highly specialized skills and facilities, and may be extremely fragile.
In the fast-moving world of commercial resource extraction it is also a very real possibility that the model will become obsolete before it is even completed. Rapidly produced, easily updated and endlessly replicable 3D printed models may overcome all of these limitations.
Elizabeth Miller, manager of environmental affairs for Seabridge Gold, says her company has been using 3D models for more than two years. “We initially developed one model for important meetings with government regulators. Based on the response . . . a second model was also created.
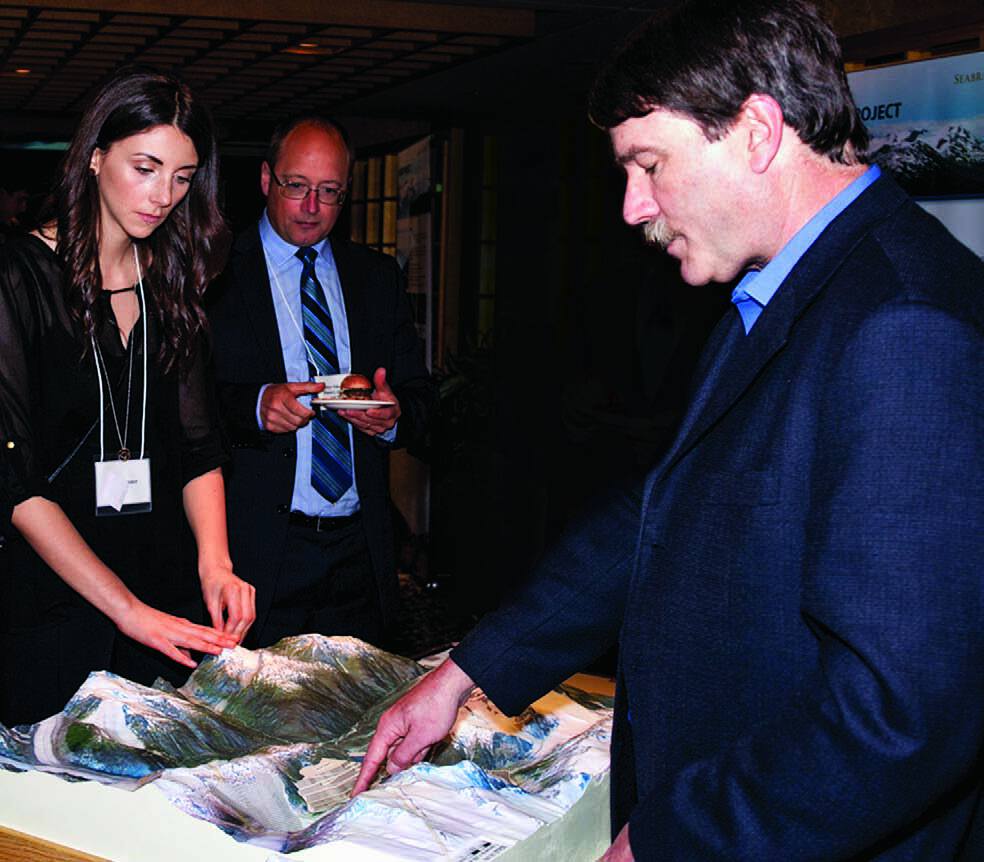
The two KSM project models have been used at numerous government regulator meetings, community meetings, open houses and trade shows. We’ve received positive feedback on the models from many Treaty and First Nations members, community members and government officials and regulators who tell us that the KSM project is much easier to imagine when its replica is presented in 3D format.”
Although current high-profile applications of 3D printing are dominated by its potential for presentation and communication, applications of a more scientific ilk are looming on the horizon. Coupling the intuitive manipulation and tactile benefits of 3D printing technology with the non-destructive analytical powers of CT scanning may allow novel investigation of complex, three-dimensional problems such as pore network analysis for oil and gas production, or fine-scale mineral relationships within mineral and metallurgical processing.
It is doubtless that more interesting and innovative applications will appear in due course, and with up-front and running costs of 3D printers tumbling every year, it may very well be that future generations come to regard the 3D printer as every bit as ubiquitous as the office photocopier is today.